There are many types of feed processing equipment, among which the key equipment that affects feed granulation is nothing more than hammer mills, mixers, and pellet machines. In today's increasingly fierce competition, many manufacturers purchase advanced production equipment, but due to incorrect operation and use, equipment failures often occur. Therefore, the correct understanding of equipment usage precautions by feed manufacturers cannot be ignored.
1. Hammer mill
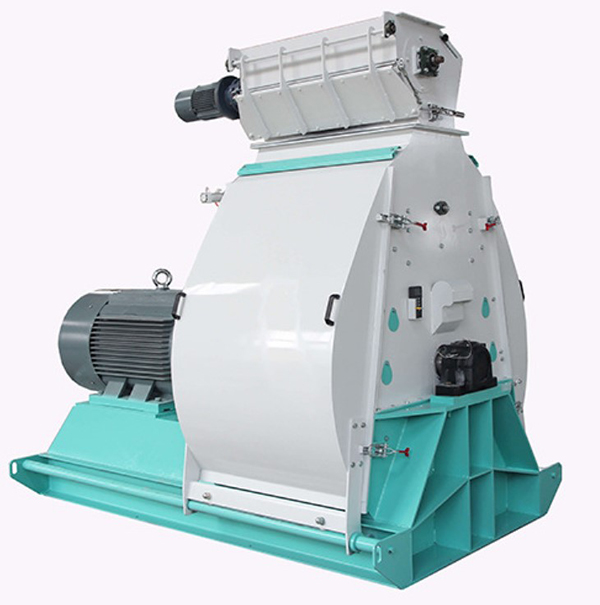
Hammer mill generally has two types: vertical and horizontal. The main components of the hammer mill are hammer and screen blades. The hammer blades should be durable, wear-resistant, and have a certain degree of toughness, arranged in a balanced manner to avoid causing equipment vibration.
Precautions for using a hammer mill:
1) Before starting the machine, check the lubrication of all connecting parts and bearings. Run the machine empty for 2-3 minutes, start feeding after normal operation, stop feeding after work is completed, and run the machine empty for 2-3 minutes. After all the materials inside the machine are drained, turn off the motor.
2) The hammer should be immediately turned around and used when worn to the centerline. If all four corners are worn to the center, a new hammer plate needs to be replaced. Attention: During replacement, the original arrangement order should not be changed, and the weight difference between each group of hammer pieces should not exceed 5g, otherwise it will affect the balance of the rotor.
3) The air network system of the hammer mill is important for improving crushing efficiency and reducing dust, and should be matched with a pulse dust collector with good performance. After each shift, clean the inside and outside of the dust collector to remove dust, and regularly inspect, clean, and lubricate the bearings.
4) The materials must not be mixed with iron blocks, crushed stones, and other debris. If abnormal sounds are heard during the work process, stop the machine in a timely manner for inspection and troubleshooting.
5) The working current and feeding amount of the feeder at the upper end of the hammer mill should be adjusted at any time according to the different materials to prevent jamming and increase the crushing amount.
2. Mixer (using paddle mixer as an example)
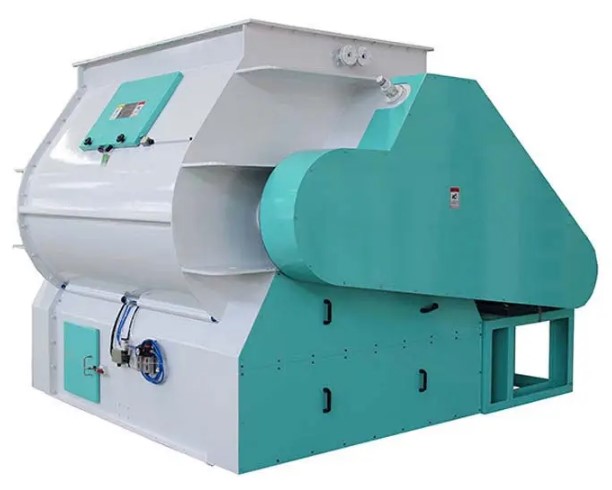
The dual axis paddle mixer is composed of a casing, rotor, cover, discharge structure, transmission device, etc. There are two rotors on the machine with opposite rotation directions. The rotor is composed of the main shaft, blade shaft, and blade. The blade shaft intersects with the main shaft cross, and the blade is welded to the blade shaft at a special angle. On the one hand, the blade with animal material rotates along the inner wall of the machine slot and moves towards the other end, causing the animal material to flip and cross shear with each other, achieving a rapid and uniform mixing effect.
Precautions for using the mixer:
1) After the main shaft rotates normally, the material should be added. Additives should be added after half of the main material enters the batch, and grease should be sprayed in after all dry materials enter the machine. After spraying and mixing for a period of time, the material can be discharged;
2) When the machine is stopped and not in use, no grease should be retained in the grease adding pipeline to avoid clogging the pipeline after solidification;
3) When mixing materials, metal impurities should not be mixed, as it may damage the rotor blades;
4) If a shutdown occurs during use, the material inside the machine should be discharged before starting the motor;
5) If there is any leakage from the discharge door, the contact between the discharge door and the sealing seat of the machine casing should be checked, such as if the discharge door is not tightly closed; The position of the travel switch should be adjusted, the adjusting nut at the bottom of the material door should be adjusted, or the sealing strip should be replaced.
3. Ring die pellet machine
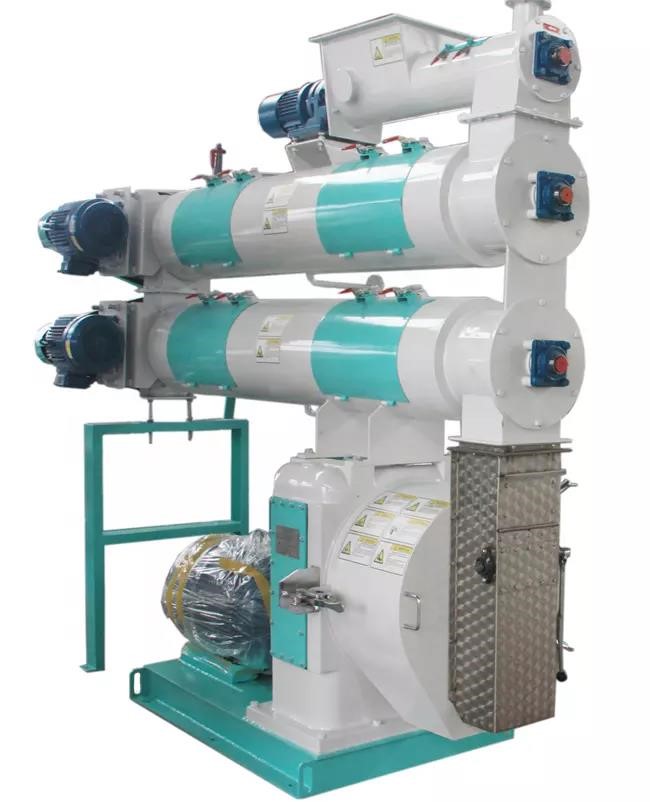
The pellet machine is a key equipment in the production process of various feed factories, and can also be said to be the heart of the feed factory. The correct use of the pellet machine directly affects the quality of the finished product.
Precautions for using the pellet machine:
1) During the production process, when too much material enters the pellet machine, causing a sudden increase in current, a manual discharge mechanism must be used for external discharge.
2) When opening the door of the pellet machine, the power must be cut off first, and the door can only be opened after the pellet machine has completely stopped running.
3) When restarting the pellet machine, it is necessary to manually rotate the pellet machine ring die (one turn) before starting the pellet machine.
4) When the machine malfunctions, the power supply must be cut off and the machine must be shut down for troubleshooting. It is strictly prohibited to use hands, feet, wooden sticks, or iron tools for hard troubleshooting during operation; It is strictly prohibited to forcefully start the motor.
5) When using a new ring die for the first time, a new pressure roller must be used. Oil can be mixed with fine sand (all passing through a 40-20 mesh sieve, with a ratio of material: oil: sand of about 6:2:1 or 6:1:1) to wash the ring die for 10 to 20 minutes, and it can be put into normal production.
6) Assist maintenance workers in inspecting and refueling the main motor bearings once a year.
7) Assist maintenance workers in changing lubricating oil for the gearbox of the pellet machine 1-2 times a year.
8) Clean the permanent magnet cylinder at least once per shift.
9) The steam pressure entering the conditioner jacket shall not exceed 1kgf/cm2.
10) The steam pressure range entering the conditioner is 2-4kgf/cm2 (generally not less than 2.5 kgf/cm2 is recommended).
11) Oil the pressure roller 2-3 times per shift.
12) Clean the feeder and conditioner 2-4 times a week (once a day in summer).
13) The distance between the cutting knife and the ring die is generally not less than 3mm.
14) During normal production, it is strictly prohibited to overload the main motor when its current exceeds the rated current.
Technical Support Contact Information:Bruce
TEL/Whatsapp/Wechat/Line : +86 18912316448
E-mail:hongyangringdie@outlook.com
Post time: Nov-15-2023